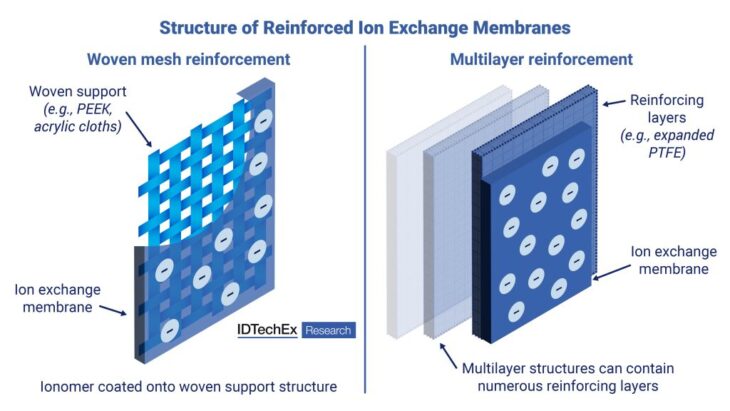
Design Trends for Next Generation Ion Exchange Membranes
Author: Dr Jack Howley, Technology Analyst at IDTechEx
Ion exchange membranes are polymer materials used as solid electrolytes in electrolysis and electrochemical applications. The ability of ion exchange membrane materials to selectively conduct ions sees them routinely employed in water treatment and chemical processing applications. IDTechEx's research report, “Ion Exchange Membranes 2025-2035: Technologies, Markets, Forecasts“, finds that ion exchange membrane demand by area will exceed 5.3 million m2 annually by 2035, driven by growing adoption in green hydrogen and redox flow battery markets.
Despite having mature market applications, ion exchange membrane material requirements are evolving. The latest membrane material design trends are heavily influenced by the performance requirements of emerging hydrogen fuel cells, water electrolyzers, and redox flow battery systems, where membranes are increasingly applied.
Key performance metrics influencing ion exchange membrane material design include conductivity, mechanical and chemical durability, and membrane thickness. Reducing the areal resistance of ion exchange membranes increases their ionic conductivity and ultimately improves the electrical energy efficiency of integrated systems. Reducing membrane film thickness may also improve conductivity while minimizing the overall membrane electrode assembly size – this is important for increasing cell density and power in applications such as hydrogen fuel cells for transport. Improving membrane materials' mechanical strength and chemical stability will be critical to enable ultrathin membrane designs, while reducing performance degradation and extending lifetime.
Major ion exchange membrane manufacturers are focusing on reinforced membranes
Reinforced membranes are emerging as the next generation of ion exchange membrane materials and present an opportunity for specialty polymer solutions. Reinforced membranes contain an ionomer in a composite material structure. Examples include woven polymer meshes or multilayer films, with polytetrafluoroethylene (PTFE), polyether ether ketone (PEEK), and polyethylene terephthalate (PET) common composite materials used. Reinforced ion exchange membranes demonstrate low swelling ratios (high dimensional stability), excellent chemical and mechanical stability, and enable the production of ultrathin films.
Woven mesh and multilayer reinforced ion exchange membranes. Source: IDTechEx
Woven mesh composite membranes show improved tensile strength while reducing membrane swelling during operation. Both perfluorosulfonic acid (PFSA) membranes, such as Nafion, and hydrocarbon membranes may be coated onto woven cloths (e.g., PEEK or PTFE) to produce composite reinforced membranes. Chemours has developed a Nafion woven composite membrane that shows improved dimensional stability with near-zero planar expansion and increased tensile strength.
Multilayer reinforcement can enhance both the mechanical and chemical stability of ion exchange membranes. Ion exchange membranes can be reinforced by sequentially coating layers of a chemically inert polymer material (e.g., expanded PTFE) onto the ionomer film. Multilayer reinforcement of PFSA proton exchange membranes unlocks tensile strengths of over 100 MPa, while as much as doubling the biaxial strength compared to non-reinforced alternatives. High mechanical stability is highly desirable for proton exchange membrane electrolyzer (PEMEL) applications, where the membrane must withstand high hydrogen pressure operation at up to 50 bar.
Manufacturers such as Gore and AGC currently offer reinforced membrane products, while a growing number of major players and start-ups alike consolidate on reinforced material designs. As of 2025, Chemours, which has conventionally not used reinforcement for applications in green hydrogen, is also exploring new reinforced membranes to complement its woven composites commercially offered for chloralkali and electrolysis applications.
Reinforcement is unlocking ultrathin ion exchange membrane designs
While reinforced membranes suffer from increased areal resistance, this can be offset by the production of ultrathin membrane films. Four-layer composite membranes demonstrate as much as a 300% increase in area-specific resistance compared to their non-reinforced counterparts. However, the increased mechanical stability afforded by reinforcement enables membrane sheet thickness to be reduced to as low as 5-10 um, increasing through-plane conductivity.
The production of ultrathin membranes also reduces the thicknesses of membrane electrode assemblies, allowing more cells to be integrated within fuel cell and electrolyzer applications. Ultrathin film membranes have the highest potential impact in hydrogen fuel cell applications, where high power density is a key requirement in mobility and transport applications.
PFAS concerns continue to drive development of hydrocarbon ion exchange membranes
Ion exchange membrane innovation does not stop at ultrathin membranes and composite designs, with the rise of PFAS-free membrane materials representing a key trend in 2025.
While perfluorinated membranes represent 85% of global annual area demand in 2025, the threat of PFAS restrictions is driving the development of alternative hydrocarbon ion exchange membrane materials. PFAS-free ion exchange membrane materials are commonly composed of polyaromatics such as polybenzimidazole (PBI) or sulfonated polyether ether ketone (SPEEK). Emerging design trends focus on supporting hydrocarbon membranes on a PEEK woven web to offer low swelling ratios and allow sheet thicknesses as low as 20 um. IDTechEx predicts that increasing adoption in green hydrogen applications, in particular anion exchange membrane electrolyzers (AEMEL), will drive the hydrocarbon ion exchange membrane market to grow at a CAGR of 22.7% by 2035.
Hydrocarbon ion exchange membrane market to grow at a CAGR of 22.7% by 2035. Source: IDTechEx
Outlook for ion exchange membranes
Ion exchange membrane materials are set to require increasingly specialized polymer solutions to meet the performance needs in key emerging green hydrogen and energy storage applications. Material innovations in membrane reinforcement show strong promise to deliver improved mechanical and chemical stability, while retaining high ionic conductivity and low film thickness.
Key players in the ion exchange market have yet to converge on one material solution, with diverse composite designs available and actively being tested in real operating conditions by customers. With the impact of PFAS restrictions still unclear, development of hydrocarbon and other PFAS alternative membranes is likely to continue, given the potential market disruption.
IDTechEx's report, “Ion Exchange Membranes 2025-2035: Technologies, Markets, Players”, forecasts that the ion exchange membrane market will exceed US$2.9B by 2035. IDTechEx's research provides technical analysis on perfluorinated and hydrocarbon ion exchange membrane technology and critical analysis of applications in emerging green hydrogen, redox flow battery, carbon capture, and storage markets.
To find out more about this IDTechEx report, including downloadable sample pages, please visit www.IDTechEx.com/iems.
For the full portfolio of advanced materials market research available from IDTechEx, please see www.IDTechEx.com/Research/AM.